Chernysheva Olga N.
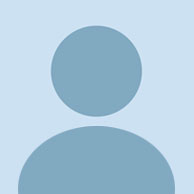
Senior Researcher, Psychologist, Department of Labor Psychology and Engineering Psychology, Faculty of Psychology
Moscow, Russia
-
Paradoxes of subjective experiences of employees in the rationalization of the subject-spatial environment in stereotypical activitiesLomonosov Psychology Journal, 2021, 2. p. 260-280read more2307
-
Relevance.People are increasingly involved in mastering new types of work. It involves rebuilding the skills developed for a variety of occupations, both mental and motor. While the problem of forming new skills is sufficiently well-developed, the problem of their restructuring has attracted significantly less attention, although, judging by the experiences of participants, it sometimes leads to a slowdown, and in some cases to the rejection of innovation process.
The purpose of this study was to identify the causes of negative effects that female employees experienced when the spatial parameters of their workplaces were rationally changed.
Methods and sampling. The study was based on the analysis of the activities of 25 seamstresses (one team) in the familiar and the rationalized subject environment. It included two additional research methods:
1) vector-coordinate method of job evaluation; 2) graphic and verbal fixation of the dynamics of how the employees subjectively assessed their psychosomatic experiences in the process of changes.
Results. The rationalization of the spatial parameters of seamstresses’ workplaces was meant for optimizing their main working posturewithout affecting the semantic component of their activity. Nevertheless, it led to certain changes in their skill of performing stereotypical movements for grinding the parts of target production. This restructuring resulted in the appearance of long-term negative experiences of somatic discomfort (from 5 to 10 days) in the process of performing labor actions. But these experiences did not correspond to the experience of somatic comfort in the main working posture taken before starting work.
Conclusion. Despite the objective improvement of the psychosomatic state of female workers, the discrepancy in the experiences of psychosomatic state in statics and dynamics is naturally and well explained from the standpoint of the Bernstein model of movement construction. It is caused by the need to change the levels of motion control and the resulting need to restructure the previously established sensory synthesis. Such a result indicates the need for psychological support of the innovation process until the end of the negative experiences associated with it.
Keywords: workplace rationalization; stereotyped activity; working posture; skill; skill restructuring; somatic comfort DOI: 10.11621/vsp.2021.02.12
-
-
Actual problems and new directions of ergonomic assessment of working conditions and ... industry.Lomonosov Psychology Journal, 2019, 1. p. 158-173read more4983
-
Relevance. Problems of injuries and dynamics of working capacity in the production are important characteristics in the analysis of work efficiency, as their assessment allows to identify the advantages and disadvantages of work organization and to identify ways to improve them. However, the existing theoretical concepts do not adequately reflect the real working conditions and work tasks of modern types and forms of work. Further research and expansion of existing concepts are required to incorporate the present findings into the practice of improving the work organization and occupational safety.
Objective. The research aim of the discussed stage was to identify key factors among working conditions and work tasks affecting occupational safety of plant employees.
Methods. The design of the study included two directions – 1) analysis of occupational injuries/errors as integral indicators of occupational safety, and 2) comparison of data gathered from previously performed legal audit of working conditions with data of real-time observations of work process. In total, 209 incidents were analyzed on the sample of 2 professional groups of employees - operators of stamping lines and drivers of forklifts.
Results.
-
The maximum frequency of injury incidents in both group happens in the period between 3d and 4th working hours in all three shifts.
-
The maximum frequency of both injury and errors surprisingly takes place during the first shift (6:00 a.m. - 14:30 p.m.): the ratio of % injuries (from the total) during the first shift to second to third is 56%:22%:3% for operators, 50%:33%:6% for drivers.
-
The key specificity of the operators’ work activity was allocated: they are constantly carrying out tactile quality control on a production line. This work task is not regarded in normative documents and in normative assessment, but is the key psychological factor of work intensity for this professional group.
Conclusion. The specificity of work tasks and conditions at modern production includes implicit factors that are not fully reflected in the regulative documents, and which require theoretical and methodological understanding by work psychology and ergonomics.
Keywords: ergonomics; occupational safety; occupational injuries; errors; tactile quality inspection DOI: 10.11621/vsp.2019.01.158 -
-